Artificial Neural Network Modeling Applied for Predicting Reformate Yield and Research Octane Number in the Reforming Process
Keywords:
Artificial Neural Network, CCRRP, Modeling, Reformate Yield, Research Octane Number, SimulationAbstract
The prediction model of the continuous catalytic regeneration reforming process was developed for
expecting the reformate yield and research octane number using an Artificial Neural Network technique (ANN) to
improve the process performance. The proposed model includes temperatures, pressures, and hydrogen to
hydrocarbon molar ratio as input parameters while the output of the process represents reformate yield and research
octane number. The ANN model was carried out to estimate the process behavior based on the LevenbergMarquardt Algorithm, which included the nine input parameters, two hidden layers (10-5 neurons), and two
parameters as network outputs. The results obtained were that the prediction error for the reformate test was 0.0027
with a regression of 0.9995, while the research octane number was 0.0026 with a regression of 0.9979. The
proposed model showed the ability of Artificial Intelligence to predict either the yield & octane number or simulate
the behavior of the process with more accurate.
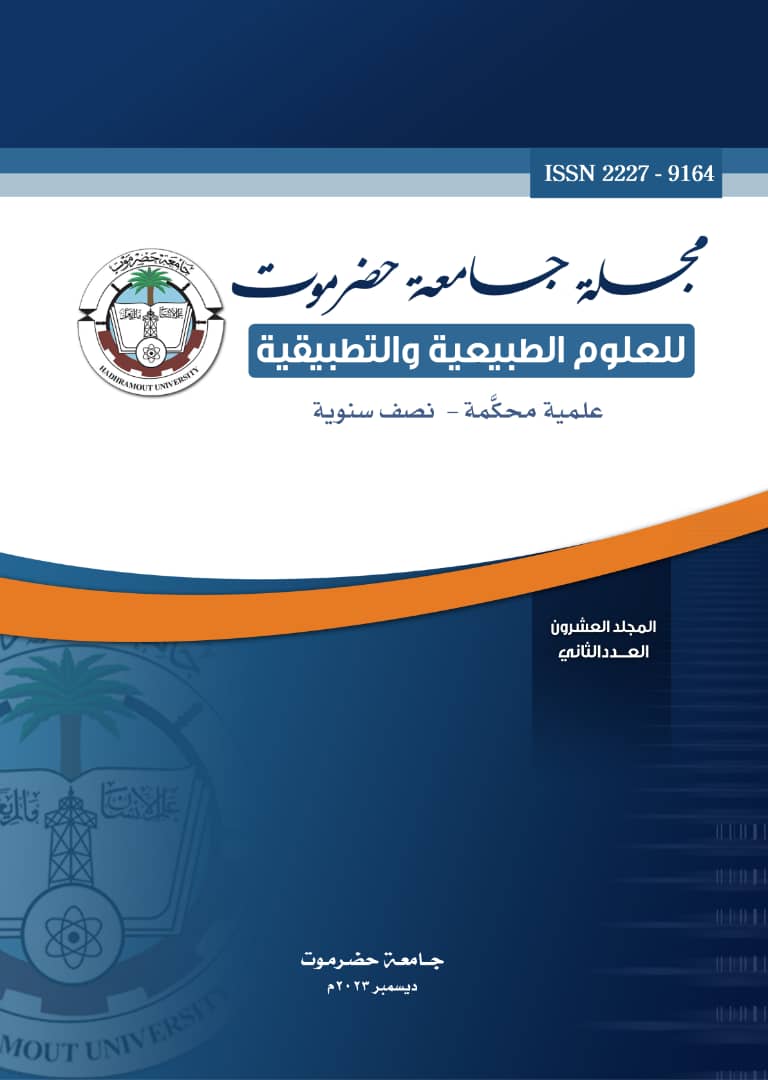